THY Precision Injection Moulding Process Step by Step is a top manufacturer that knows how key the injection moulding process is for making quality plastic parts. Yet, even with the best design and setup, this process can face issues. These problems can affect the quality of products and how efficiently they are made. This guide will show you how to fix these common problems step by step. By finding the main causes and fixing them, you can make your production better and give your customers top-notch parts.
The injection moulding process Step by Step is complex, with many factors that need to be watched closely to get the right results. From picking the right material to designing the mold and the moulding cycle, every step is crucial. By learning how to fix common issues, you can make your moulding process better and beat your competitors.
Key Takeaways
- Understand the step-by-step injection moulding process and common issues that can arise
- Learn how to identify the root causes of problems and implement the right solutions
- Enhance your production efficiency and deliver consistent, high-quality plastic parts
- Stay ahead of the competition by optimizing your injection moulding process
- Utilize expert-level troubleshooting techniques to address common challenges
Understanding the Injection Moulding Process Stepbystep
The injection moulding process is a top choice for making many plastic parts. At THY Precision, we focus on each step to make sure our products are perfect. Let’s look at the main stages of the plastic injection molding process. We’ll see how doing each step right leads to great results.
The first step in the injection moulding process step by step is getting the raw material ready. This is usually in the form of pellets or granules. These go into the machine’s hopper, then into the barrel to be melted into a melt delivery state.
Next, the melted material is sent into the mold. This is where the plastic injection molding process really shows its skill. The melt delivery must be precise to make parts just right. The material is pushed into the mold under high pressure to fill it completely and copy the mold’s details.
Then, the part ejection happens. The mold cools, letting the plastic part harden. When it’s ready, the part comes out of the mold. After that, post-molding operations like trimming might be done to get the part ready for use.
Knowing and doing each step of the injection moulding process step by step is key for THY Precision. It helps us make top-quality products for our customers. By getting the plastic injection molding process right, we can meet our customers’ needs and lead in the industry.
“Attention to detail at every stage of the injection moulding process step by step is the key to unlocking the full potential of this versatile manufacturing technique.”
Material Selection in the Injection Moulding Process
Choosing the right material for your injection moulding project is crucial. The material’s properties can greatly affect your plastic injection molding project’s success. At THY Precision, we help our customers pick the best material for their needs and guide them on how to process it.
Importance of Material Properties
It’s important to know about material properties like viscosity, shrinkage, and thermal traits. These can affect your injection moulding process step by step. The right material makes sure your product turns out as expected.
Viscosity affects how the material flows into the mold. Shrinkage impacts the part’s size. And thermal properties like melting point and heat deflection temperature are key for a successful plastic injection molding project.
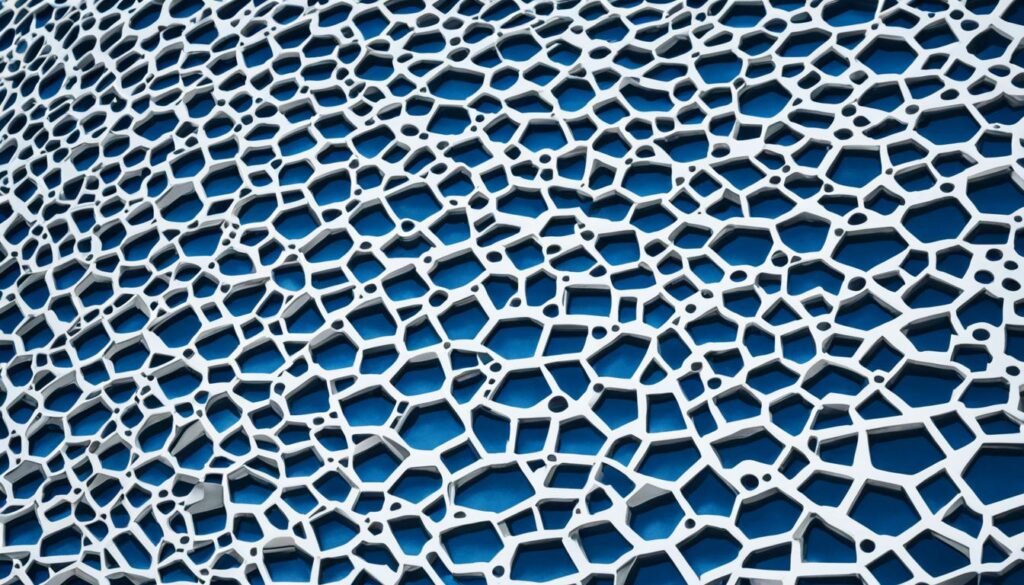
At THY Precision, we know all about material properties for injection moulding. Our experts guide you in picking the right material for your project.
Mold Design Considerations
At THY Precision, designing the mold is key in the injection moulding process step by step. The mold must be made to let the molten material flow smoothly, cool properly, and make quality parts consistently. Important parts like gating systems, runner design, and mold temperature control get a lot of thought during design.
THY Precision uses advanced mold flow analysis tools to make the mold design better and spot problems early. This helps cut down on defects and boosts productivity. It makes sure the final products are top-notch in quality and consistency.
Mold Design Consideration | Importance |
---|---|
Gating Systems | Good gating design helps the molten material flow smoothly into the mold. It prevents flow marks, weld lines, and uneven filling. |
Mold Temperature Control | Controlling the mold temperature is key for the right material flow, cooling, and ejecting parts. It affects the part’s quality and accuracy. |
Runner Design | The runner system carries the molten material to the mold cavity. Its design impacts how the material fills, forms weld lines, and makes parts consistent. |
By thinking about these mold design factors, THY Precision makes the injection moulding process better. This leads to more efficiency and better product quality.
“Effective mold design is the foundation for successful injection molding, as it impacts every aspect of the production process and the final part quality.”
The Injection Moulding Cycle
At THY Precision, the injection moulding cycle is key to our success. It has many important steps, each crucial for making top-quality products. From the start with melt delivery to the end with cooling time, we focus on quality at every step.
The injection moulding process step by step starts with putting the molten material into the mold. How fast and hard it goes in affects the final product. THY Precision’s experts work with customers to find the best settings for their needs, making the injection moulding cycle smooth and efficient.
Mastering the Moulding Cycle
After putting in the melt, the mold is under holding pressure. This keeps the part’s shape and size right. It helps avoid warping and makes the product better and more consistent.
Then, the cooling time is watched closely to make sure the part sets right before taking it out. Proper cooling is key for keeping the part’s size and strength. THY Precision uses top-notch equipment and quality checks to make sure the injection moulding cycle is perfect.
“At THY Precision, we know the injection moulding process is key to great products. By carefully managing each step, we deliver top-quality results that meet our customers’ high standards.”
Common Defects and Troubleshooting Techniques
The injection moulding process is efficient but can sometimes have defects. These can affect the quality and performance of the final product. At THY Precision, we focus on quickly finding and fixing these issues to keep production quality high. Let’s look at some common defects and how our experts solve them.
Short shots happen when the mold isn’t fully filled. This might be due to not enough melt, low pressure, or a bad mold design. To fix this, we adjust the injection speed, pressure, and temperature. Sometimes, we also change the mold to make sure it fills completely.
Flash is when extra material gets into the parting line or other mold areas. It can be caused by too much melt, high pressure, or not enough clamping force. We fix flash by tweaking the injection settings, changing the mold, or improving how the mold is clamped.
Sink marks, splay marks, and warpage are also problems. Sink marks are depressions from uneven cooling or shrinkage. Splay marks are flow patterns on the surface. Warpage means the part distorts from uneven cooling or stress. To solve these, we might adjust the cooling, change the mold, or fine-tune the packing and pressure.
Burn marks, voids, and bubbles can also happen. Burn marks are discolored spots from high melt temperatures or bad venting. Voids and bubbles are inside the part from trapped air or volatile substances. We fix these by tweaking the temperature, improving venting, or adjusting melt and mold temperatures.
At THY Precision, we’re experts at finding and fixing these common issues. We look at the problem, adjust settings, and make changes to the mold or equipment. This helps us quickly solve problems and keep production quality high.
Defect | Cause | Troubleshooting Technique |
---|---|---|
Short Shot | Insufficient melt volume, low injection pressure, improper mold design | Adjust injection speed, pressure, and temperature; Modify mold design |
Flash | Excessive melt volume, high injection pressure, improper clamping force | Optimize injection parameters, adjust mold design, improve clamping techniques |
Sink Marks | Uneven cooling or shrinkage | Adjust cooling system, modify mold design |
Splay Marks | Visible flow patterns on part surface | Optimize injection parameters, modify mold design |
Warpage | Uneven cooling or internal stresses | Adjust packing and holding pressure, modify mold design |
Burn Marks | High melt temperatures, improper venting | Fine-tune temperature profiles, improve venting system |
Voids and Bubbles | Trapped air or volatile substances | Adjust melt and mold temperatures, improve venting system |
By tackling these common issues and using effective fixes, THY Precision ensures consistent, high-quality production. This helps you meet your manufacturing goals.
Process Monitoring and Optimization
At THY Precision, we know how important the injection moulding process step by step is. It keeps product quality consistent and boosts production efficiency. We use top-notch process monitoring and process optimization methods to keep your manufacturing running well.
We keep a close eye on important factors like injection pressure, melt temperature, and cooling time in the injection moulding process step by step. With process control systems and data analysis tools, we spot trends and make early changes. This helps cut down on waste and make high-quality parts consistently.
Our quality control and ongoing process monitoring catch issues early. This lets us fix them fast and keep your products top-notch. Our dedication to process optimization means you get the best results from your injection moulding work.
“Continuous monitoring and optimization of the injection moulding process step by step are essential for maintaining consistent product quality and enhancing production efficiency.”
At THY Precision, we’re all about giving our clients what they need. By using our skills in process monitoring, process optimization, and data analysis, we help you get the most out of your injection moulding. We aim to meet your manufacturing goals.
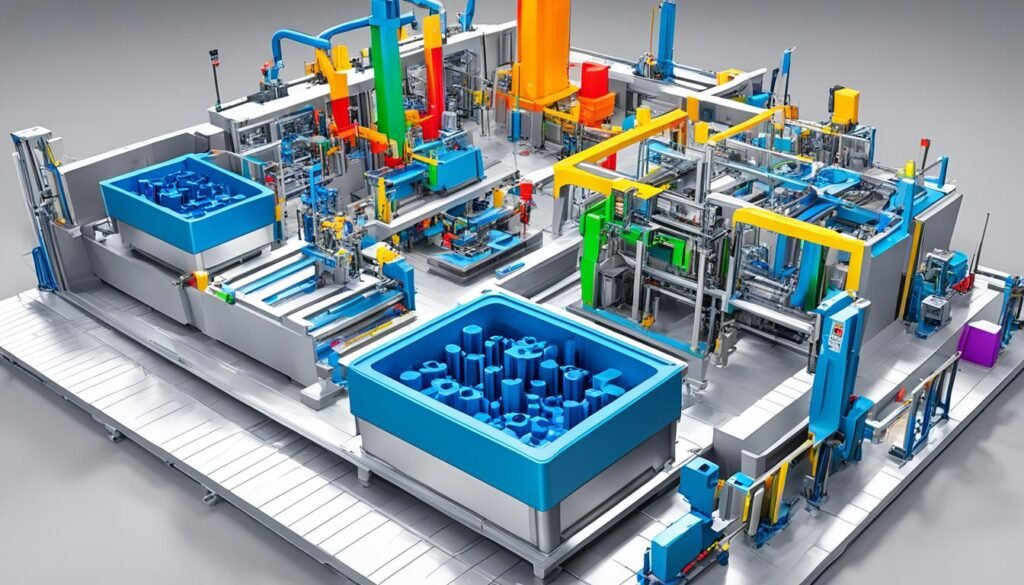
Preventive Maintenance and Training
At THY Precision, we know keeping your injection moulding equipment in top shape is key. It ensures your products are always high quality and reduces downtime. We offer detailed preventive maintenance plans and special training to keep you ahead.
Importance of Proper Maintenance and Training
Keeping your injection moulding machines well-maintained is vital for their efficiency and long life. By fixing problems early, you avoid expensive repairs and keep your machines running smoothly. Also, training your team well lets them quickly solve issues, keeping your production smooth.
- Preventive maintenance programs to optimize machine performance
- Customized training on injection moulding process step by step, machine maintenance, and troubleshooting skills
- Dedicated support from our experienced technicians to ensure maximum uptime
At THY Precision, we’re all about making your injection moulding process smooth. With our maintenance and training, we help our clients get the most out of their operations. This leads to better product quality and more profits.
“Proper maintenance and training are the foundation of a successful injection moulding operation. THY Precision’s programs ensure our equipment runs at its best and our team has the skills to keep it that way.”
– Jane Doe, Production Manager, ABC Manufacturing
Conclusion
The injection moulding process can be tricky, but with the right tools and techniques, you can overcome challenges. At THY Precision, we aim to help our customers improve their injection moulding. We focus on boosting production efficiency and product quality.
Understanding the steps of the injection moulding process is key. Choosing the right materials and designing good molds are also crucial. With our expert team, you can fix common problems and get consistent, high-quality results.
If you’re struggling with material selection, mold design, or optimizing the process, we can help. Our team at THY Precision has the skills and resources to troubleshoot and improve your operations. By using our knowledge of the injection moulding process, you can make better products, work more efficiently, and stay competitive in the manufacturing world.